First In Industry
CRUNCH CFD was the first CFD code to accurately predict dynamic effects of cavitation instabilities on pump performance. Cavitation instabilities such as rotational cavitation generate high amplitude fluctuating pressure loads on blade tips and create large dynamic loads on the shaft that can lead to bearing failure. Furthermore identifying and quantifying is expensive and not part of routine pump performance testing. The ability to predict these dynamics provides pump designers with an advanced tool that can be used to characterize pump designs early in the design cycle and rectify them if necessary.
Validation for rotational cavitation instability for the low pressure axial pump (inducer) in the Space Shuttle Main Engine (SSME) is illustrated. Cavitation instability occurs when NPSH drops to a level where the cavity on one blade interacts with the neighboring blade and creates an instability. The instability results in the cavity rotating relative to the blades creating fluctuating loads on the blades and flowfield asymmetry as seen here. The instability frequency and energy level is accurately predicted. The simulations also provide the rotating load on the shaft due to the asymetrical cavitation resulting from the instability.

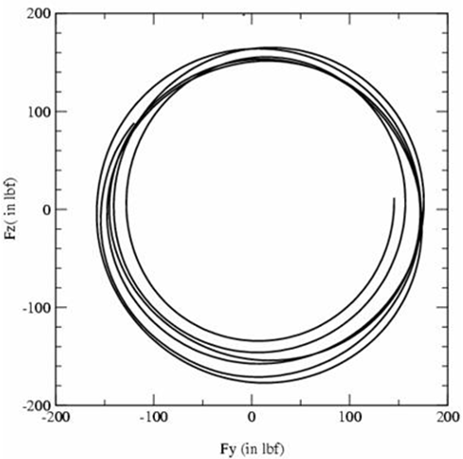
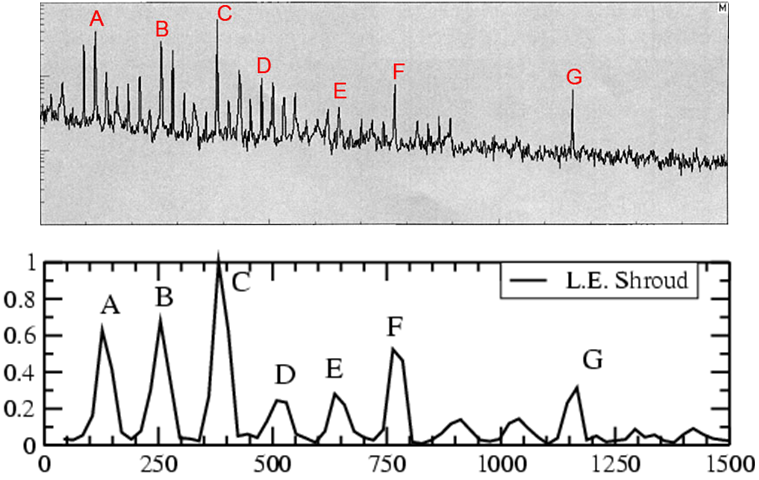